2 minute read
Batteries: Best practice
1. Initiate a battery testing regime
Ecobat Battery has found that 27% of vehicles that enter the independent workshop need either their batteries recharged or reconditioned, and a further 11% need a replacement, which means that almost 40% of the vehicles they service daily have a battery issue.
However, whether the vehicle is booked in for an MOT, annual service, or some sort of repair, workshops rarely test the voltage of the battery, let alone its condition. The knock-on effect is that 40% of roadside breakdowns are due to battery failure and the beneficiaries of these failures are not independent workshops, or the factors that supply them, but breakdown services such as the AA and RAC.
3. Ensure the correct voltage to the vehicle’s electrical system is maintained during battery replacement and support the vehicle’s battery when running diagnostics
2.
Reset the vehicle’s ECU after an AGM or EFB start/stop battery has been replaced
Unless the vehicle has been modified and requires an upgraded battery, technicians should always ensure they install a replacement of the same standard as the vehicle’s OE fitment, so if it’s an AGM or EFB battery at first fit, the replacement should be the same. However, if a higher capacity battery is required, it is possible to replace an EFB with an AGM version, but remember, an AGM cannot be replaced by an EFB and, irrespective of the type, both need to be reprogrammed into the vehicle’s energy management system.
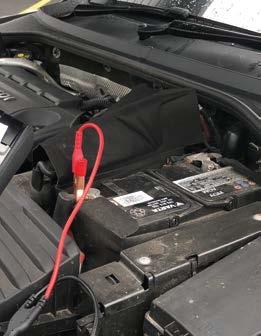
This is important because an aged battery at the end of its life, behaves differently when it comes to its available capacity, energy output and charge acceptance, than a new, unused one. The BMS (battery management system), together with the EBS (electronic battery sensor) monitor the battery over its lifetime, detecting the number of engine starts and the energy flow (Ah throughput), monitoring the state of charge, controlling the charging and adapting the energy management of the battery, dependent on its state of health.
If this reprogramming is not carried out correctly it can cause issues with, or even failure of, the start/stop function, which can increase fuel consumption and also affect the vehicle’s comfort functions.
These procedures are linked, as to prevent causing unnecessary problems and to be carried out effectively, they both require a stable source of power to be constantly supplied to the vehicle’s electrical system. Although, because of the wellknown risk of losing stored memory data, this may seem obvious when changing the battery, it’s not quite so apparent when it comes to undertaking diagnostic processes. However, maintaining the correct voltage during extensive periods of troubleshooting is very important, as it helps technicians to correctly identify the underlying fault. This is because during diagnostic procedures, which nowadays are commonplace, the engine is switched off, but power is still drawn from the battery.
When carrying out prolonged diagnosis, the vehicle’s control units and other electrical equipment can discharge the battery to such an extent that the on-board system voltage falls below the permissible voltage limit of the control units and a corresponding entry is made in the fault memory, and data can be lost (steering angle sensor, end positions of the electric window lifters etc.).
Using equipment dedicated to battery support is now a necessity in any workshop. A battery performs best when it’s in peak condition, so by reducing the possibility of battery failure in the workshop, or even worse after the customer gets home, workshops can save more than time and money, they can preserve their reputation.
https://ecobat.com/our-business/ecobat-battery/